Advanced Renesis tech
#154
Ayrton Senna Forever
You wrote this RG: "The rounded shape of the seal tip allows gasoline to get under it. As it rotates and tries to compress the air, this added pressure will also be in the gasoline under the seal. This will exert pressure on the apex seal trying to push it into it's groove."
My new question is connecting to my last: If is this "pushing into the groove the apex" is an issue, why is this just at starting the engine?..so if the combustion pressure can push back the apex to its groove (as you said), it has to be an issue when the engine is working, too. What is the difference between when there are gasoline (at cold starting)is under the apex, or oil, or just "air/gasoline mix" with pressure? I hope you understand what I mean.
...and why is enough to use this weaker springs if the lighter apex is pushed by less centripetal force to the trochoid wall (at higher rpms), than the heavier RX-7 apex....and how can we avoid always the compression losting with that weaker apex springs, if it's an issue at starting.
My new question is connecting to my last: If is this "pushing into the groove the apex" is an issue, why is this just at starting the engine?..so if the combustion pressure can push back the apex to its groove (as you said), it has to be an issue when the engine is working, too. What is the difference between when there are gasoline (at cold starting)is under the apex, or oil, or just "air/gasoline mix" with pressure? I hope you understand what I mean.
...and why is enough to use this weaker springs if the lighter apex is pushed by less centripetal force to the trochoid wall (at higher rpms), than the heavier RX-7 apex....and how can we avoid always the compression losting with that weaker apex springs, if it's an issue at starting.
#155
Registered
Thread Starter
Lower rpm's is where you can have issues. At low rpm's, there isn't much force trying to hold the apex seals outward. Just spring pressure. As the engine rotates faster and faster, you have forces on the apex seal in 2 directions. Towards the housings but also towards the back of the apex seal grooves. Some pressure gets under the seal as well to help hold it outward. There is enough force to easily overcome combustion pressures. Fuel is better distributed and atomized at higher rpms and doesn't ahve te tendency to get under the seals. A cold engine can't atomize fuel easily so it has more of a tendency to pool on the surfaces and this will build up under the apex seals. Combine this with relatively little pressure holding the seals against the housings and it'll flood easier.
#156
Registered
iTrader: (3)
further on the leading edges issue--has anyone ever measured them out? Maybe they are off just a tad? Even CNC can be minutely off. IF ----there are some inconsistances, it would be interesting in addressing. In 2 ways. In addressing the exact match of each face of one rotor AND the insuring that the 2nd rotor exactly matches the 1st. The ecu controls each rotor the same-- so if any of the faces dont exactly match in distance from the leading edge then there is room for improvement.
OD
OD
#157
Ayrton Senna Forever
Originally Posted by rotarygod
Lower rpm's is where you can have issues. At low rpm's, there isn't much force trying to hold the apex seals outward. Just spring pressure. As the engine rotates faster and faster, you have forces on the apex seal in 2 directions. Towards the housings but also towards the back of the apex seal grooves. Some pressure gets under the seal as well to help hold it outward. There is enough force to easily overcome combustion pressures. Fuel is better distributed and atomized at higher rpms and doesn't ahve te tendency to get under the seals. A cold engine can't atomize fuel easily so it has more of a tendency to pool on the surfaces and this will build up under the apex seals. Combine this with relatively little pressure holding the seals against the housings and it'll flood easier.
Last edited by ayrton012; 11-08-2006 at 02:21 AM.
#158
Originally Posted by shaunv74
I think ceramic rotors would be a better route than Titanium. You don't have to worry about them catching fire, .

#159
Registered
Thread Starter
Heat is always being transferred to both the coolant and the oil systems. The temps of the rotors never exceeds about 450*F or so in spots. Titanium has a MUCH higher flash point than that and even Magnesium won't ignite at that level.
#160
Registered User
Join Date: Oct 2005
Location: Toronto, Canada
Posts: 2,047
Likes: 0
Received 0 Likes
on
0 Posts
Last edited by Renesis_8; 09-11-2011 at 10:32 AM.
#161
Lasse wankel
Join Date: Aug 2006
Location: Stockholm,Sweden
Posts: 164
Likes: 0
Received 0 Likes
on
0 Posts
I have only measured the 1974-1978 9:2 cr rotors and they were 1-2 mm apart from face to face. Right now i have 12 9:0 cr rotors and i shall when time allows carefully measure the bathtube chambers to apex seal groove.
/Lasse
/Lasse
#162
Power!!
In my manufacturing experience we've had milling machines burn up dry machining magnesium gear box housings because a chip got too hot, caught fire, and landed in a chip conveyor full of magnesium chips.
When designing jet engines for Pratt & Whitney we didn't use titanium alloys in temps above 800 degrees F and never in the combuster and turbine sections of the engine. I've looked at the remains of test stand engines where the titanium compressor blades got too hot and caught fire. It was nasty and quick.
I don't know what the guys in NASCAR do but I know from my personal experience what not to do with Titanium alloys.
When designing jet engines for Pratt & Whitney we didn't use titanium alloys in temps above 800 degrees F and never in the combuster and turbine sections of the engine. I've looked at the remains of test stand engines where the titanium compressor blades got too hot and caught fire. It was nasty and quick.
I don't know what the guys in NASCAR do but I know from my personal experience what not to do with Titanium alloys.
#164
Titanium Valves
With over 25 years of experience in the manufacturing of titanium products, the Del West brand represents the worldwide standard for advanced titanium valve technology. Every aspect of the design and production of Del West titanium valves clearly sets us apart from the rest of the industry. No other titanium valvetrain manufacturer can claim an association with more championships in every major professional racing series worldwide, including Formula 1, CART, IRL, NASCAR, WRC, Trans-Am, World Superbike, off-road racing, NHRA/IHRA, offshore marine and more!
All valves are completely CNC machined and precision ground. All critical dimensions of the valves are controlled 100% for visual and dimensional aspects before shipment.
Del West applies in-house developed thermally sprayed coatings to protect against wear on the stem. The tip of the valve is protected by either the insertion of a steel tip or with a thermally sprayed coating.
Del West can apply thin film coatings such as Physical and Chemical Vapor Deposition (PVD, CVD). These types of coatings include Diamond-Like Carbon (DLC), Titanium Nitride (TiN), and Chromium Nitride (CrN). They are recommended to be applied to any surface of a component where increased wear protection and extended service are required. A Del West engineer can help guide you on the performance benefits to applying these coatings.
100% traceability on all components from receipt of material to shipment of product is maintained at Del West.
The lower mass of the titanium valves combined with the matching Del West keepers (locks, cotters) and spring retainers allow for the use of higher RPM and more aggressive cam profiles without the loss of valve control. This results in the development of broader torque curves with increased horsepower and higher RPM and power numbers.
Looks like we need to also call F1, CART, IRL etc etc.
With over 25 years of experience in the manufacturing of titanium products, the Del West brand represents the worldwide standard for advanced titanium valve technology. Every aspect of the design and production of Del West titanium valves clearly sets us apart from the rest of the industry. No other titanium valvetrain manufacturer can claim an association with more championships in every major professional racing series worldwide, including Formula 1, CART, IRL, NASCAR, WRC, Trans-Am, World Superbike, off-road racing, NHRA/IHRA, offshore marine and more!
All valves are completely CNC machined and precision ground. All critical dimensions of the valves are controlled 100% for visual and dimensional aspects before shipment.
Del West applies in-house developed thermally sprayed coatings to protect against wear on the stem. The tip of the valve is protected by either the insertion of a steel tip or with a thermally sprayed coating.
Del West can apply thin film coatings such as Physical and Chemical Vapor Deposition (PVD, CVD). These types of coatings include Diamond-Like Carbon (DLC), Titanium Nitride (TiN), and Chromium Nitride (CrN). They are recommended to be applied to any surface of a component where increased wear protection and extended service are required. A Del West engineer can help guide you on the performance benefits to applying these coatings.
100% traceability on all components from receipt of material to shipment of product is maintained at Del West.
The lower mass of the titanium valves combined with the matching Del West keepers (locks, cotters) and spring retainers allow for the use of higher RPM and more aggressive cam profiles without the loss of valve control. This results in the development of broader torque curves with increased horsepower and higher RPM and power numbers.
Looks like we need to also call F1, CART, IRL etc etc.

#165
To RotaryGod and others, this is an awesome thread. I'm learning a lot, thanks.
To me the problem with the Renesis is not about its advantages or disadvantages with the 13B. The Renesis is, overall, the superior engine. And it should be, as it came later.
To me, Mazda mistake was not in the engineering, but with common sense and understanding its market. The Renesis is a rotary masterpiece, had Mazda implemented its introduction better or make a few different decisions at key points in its development, it would have simply ruled over everything in it class. As it is, the RX-8 is doing a good job, but it could have done even better.
The problem is that it appears Mazda did not anticipate the need for a higher performance engine that used FI. Mazda should have anticipated this even if the present RX-8 really put out 280 HP to 250 HP at the crank (which it doesn't without mods). This is because their last generation RX-7 turbos were in the 280 HP range and were lighter cars. People would naturally expect improvements over the last RX-7s or demand higher performance relative to the competition. If you know that you are producing an heavier car that can seat 4 people, than you should know that you need more horsepower. If you know that you are not going to meet a certain HP goal with NA, than you should know to prepare to go FI.
The common sense mark would be to introduce a FI version of the Renesis at 300 HP crank. Even if it was going for $5,000 to $7,500 more, it would have been a hit. Mazda could have simply adjusted production numbers of the FI Renesis and the NA Renesis based on customer demand. Why would Mazda not do something that seems so logical?
Also coming out with a 4 port and 6 port engine, seemed a bit of a waste to me. By having just a 6 port engine, you have a STANDARD engine. You are making most things in the Auto and MT interchangeable and reducing cost and decreasing performance variances.
Just to have produced a 4 port and to de-tune it, was a bit nutty to me. Think about all that wasted effort and energy. Why go out of your way to DE-TUNE an engine and go cheap on parts (no 2nd oil cooler, inadequate ATF cooler, etc...)? A standard 6 port engine, at the very beginning, would allow you to focus more energy on FI development of that engine and save money.
It would have been better for Mazda techs to have figured out the FI issue, during the R&D phase of the Renesis. This says to me, that perhaps the ultimate HP numbers of the renesis were overestimated long before emissions became an issue on the production models. Maybe Mazda techs though they could hit 280 HP or above, but a combination of issue caught up to them and prevented the Renesis from seeing those number in it NA form. This could also explain why nobody brought up the issue of going FI earlier, since they may have thought that the NA Renesis would put out higher HP numbers. Yes, the NA Renesis puts out higher numbers than an NA 13B, put you need to factor in weight and competing cars in its class. Again, making it obvious that if the NA Renesis did not hit a target HP that you should consider FI and think about that during R&D or during the early production phase.
Also, the Mazda ECU appears odd to me for a couple of reasons. It was if they never anticipated going for higher performance gains and an aftermarket. The ECU seemed to become important when it came to emissions, and a "hack" was thought of. A lot could have been done by having an easy to tune and program ECU. Eventually, people will crack the ECU and make better flashes, but it will be Pro-Tuners and not Mazda Techs. Same goes for FI, it will be Pro-Tuners that get the Renesis to really soar and not Mazda or Mazdaspeed. That is outrageous, when you think about it.
To me the problem with the Renesis is not about its advantages or disadvantages with the 13B. The Renesis is, overall, the superior engine. And it should be, as it came later.
To me, Mazda mistake was not in the engineering, but with common sense and understanding its market. The Renesis is a rotary masterpiece, had Mazda implemented its introduction better or make a few different decisions at key points in its development, it would have simply ruled over everything in it class. As it is, the RX-8 is doing a good job, but it could have done even better.
The problem is that it appears Mazda did not anticipate the need for a higher performance engine that used FI. Mazda should have anticipated this even if the present RX-8 really put out 280 HP to 250 HP at the crank (which it doesn't without mods). This is because their last generation RX-7 turbos were in the 280 HP range and were lighter cars. People would naturally expect improvements over the last RX-7s or demand higher performance relative to the competition. If you know that you are producing an heavier car that can seat 4 people, than you should know that you need more horsepower. If you know that you are not going to meet a certain HP goal with NA, than you should know to prepare to go FI.
The common sense mark would be to introduce a FI version of the Renesis at 300 HP crank. Even if it was going for $5,000 to $7,500 more, it would have been a hit. Mazda could have simply adjusted production numbers of the FI Renesis and the NA Renesis based on customer demand. Why would Mazda not do something that seems so logical?
Also coming out with a 4 port and 6 port engine, seemed a bit of a waste to me. By having just a 6 port engine, you have a STANDARD engine. You are making most things in the Auto and MT interchangeable and reducing cost and decreasing performance variances.
Just to have produced a 4 port and to de-tune it, was a bit nutty to me. Think about all that wasted effort and energy. Why go out of your way to DE-TUNE an engine and go cheap on parts (no 2nd oil cooler, inadequate ATF cooler, etc...)? A standard 6 port engine, at the very beginning, would allow you to focus more energy on FI development of that engine and save money.
It would have been better for Mazda techs to have figured out the FI issue, during the R&D phase of the Renesis. This says to me, that perhaps the ultimate HP numbers of the renesis were overestimated long before emissions became an issue on the production models. Maybe Mazda techs though they could hit 280 HP or above, but a combination of issue caught up to them and prevented the Renesis from seeing those number in it NA form. This could also explain why nobody brought up the issue of going FI earlier, since they may have thought that the NA Renesis would put out higher HP numbers. Yes, the NA Renesis puts out higher numbers than an NA 13B, put you need to factor in weight and competing cars in its class. Again, making it obvious that if the NA Renesis did not hit a target HP that you should consider FI and think about that during R&D or during the early production phase.
Also, the Mazda ECU appears odd to me for a couple of reasons. It was if they never anticipated going for higher performance gains and an aftermarket. The ECU seemed to become important when it came to emissions, and a "hack" was thought of. A lot could have been done by having an easy to tune and program ECU. Eventually, people will crack the ECU and make better flashes, but it will be Pro-Tuners and not Mazda Techs. Same goes for FI, it will be Pro-Tuners that get the Renesis to really soar and not Mazda or Mazdaspeed. That is outrageous, when you think about it.
Last edited by sosonic; 11-08-2006 at 08:19 PM.
#166
Registered User
Join Date: Oct 2005
Location: Toronto, Canada
Posts: 2,047
Likes: 0
Received 0 Likes
on
0 Posts
After reading about the horsepower speedsource cars make, I think the next generation Renesis will be able to make 280-300HP crank in NA form. Some of the things discussed in this thread arent that hard for Mazda to put into production. Direct Injection (better emissions, more power), lighter housings (lower weight), *possibly* lighter rotors (more power, higher rpm), also rework the exhaust ports to flow better (more horsepower everywhere, especially high rpm).
DI will definatly make it into an rotary engine. I am sure of it.
Put this motor in a 2 seater, it'll do low to mid-5s 0-60 consistently.
________
Club Royal Condominium
DI will definatly make it into an rotary engine. I am sure of it.
Put this motor in a 2 seater, it'll do low to mid-5s 0-60 consistently.
________
Club Royal Condominium
Last edited by Renesis_8; 09-11-2011 at 10:33 AM.
#167
jersey fresh
Join Date: Dec 2005
Location: Boston, MA
Posts: 3,688
Likes: 0
Received 0 Likes
on
0 Posts
I agree with a non turbo, lighter material and DI future. Aluminum house and rotors, not sure about the Eshaft.
direct injection question:
in the mazda disi engine the fuel psi is at or around 1600, would this be a suitable psi for a DI rotary??
also would the combustion face have to be redesigned in order to flow the vapor over the spark plugs in a more controlled manner or would it be control via injector placement?
direct injection question:
in the mazda disi engine the fuel psi is at or around 1600, would this be a suitable psi for a DI rotary??
also would the combustion face have to be redesigned in order to flow the vapor over the spark plugs in a more controlled manner or would it be control via injector placement?
#168
Registered User
Join Date: Oct 2005
Location: Toronto, Canada
Posts: 2,047
Likes: 0
Received 0 Likes
on
0 Posts
Last edited by Renesis_8; 09-11-2011 at 10:34 AM.
#169
Registered
Thread Starter
The DISI engine runs 1800 psi of fuel pressure. I nkow the person who is wokring on DI with Mazda and he's here in the U.S. Unfortunately he won't tell me much as it's not his info to pass along but he did say the biggest challenge right now is getting the fuel pressure he wants. Remember the RX-8 runs somewhere between 38-43 psi of fuel pressure. I don't remember exactly but it's not far off. The DISI engine runs 1800 psi. He wants over 20,000 psi of fuel pressure!!! That's new common rail diesel pressures. The problem is with getting that pressure.
Logic would say to use a diesel style pump. This won't work. Those pumps are mechanical and are lubed by the fuel going through them. Diesel fuel is an oil. It lubricates. Gasoline doesn't. We'd burn up pumps. We also can't just make a pump that is lubed off of engine oil as the pressure differetial on the pump seals would be nearly 20,000 psi. The seals would fail immediately. That's the biggest thing holding it back.
They can make DI work on a rotary now but it is limited in it's abilities and not really worth putting into production at this time. They are working on it though. An interesting tidbit is that fuel injector location has a huge effect on fuel pressures required to do the job properly. Think about that one for a while.
Logic would say to use a diesel style pump. This won't work. Those pumps are mechanical and are lubed by the fuel going through them. Diesel fuel is an oil. It lubricates. Gasoline doesn't. We'd burn up pumps. We also can't just make a pump that is lubed off of engine oil as the pressure differetial on the pump seals would be nearly 20,000 psi. The seals would fail immediately. That's the biggest thing holding it back.
They can make DI work on a rotary now but it is limited in it's abilities and not really worth putting into production at this time. They are working on it though. An interesting tidbit is that fuel injector location has a huge effect on fuel pressures required to do the job properly. Think about that one for a while.
#170
Registered User
Join Date: Oct 2005
Location: Toronto, Canada
Posts: 2,047
Likes: 0
Received 0 Likes
on
0 Posts
Maybe the rotary should make the switch to diesel!! its fast burning too!. Spark ignited diesel rotary.
________
Avandia Lawsuit
________
Avandia Lawsuit
Last edited by Renesis_8; 09-11-2011 at 10:34 AM.
#172
Go Texas Longhorns!
earlier experiments on DI rotary's were done with low pressure fuel injectors and were found to be sucessful at some levels. The ultra high pressure idea is needed if your going to inject the fuel right into the chamber between the spark plugs.
I'm still collecting the SAE papers on the subject.
I'm still collecting the SAE papers on the subject.
#174
jersey fresh
Join Date: Dec 2005
Location: Boston, MA
Posts: 3,688
Likes: 0
Received 0 Likes
on
0 Posts
i believe the injector location for a tradition piston DI engine is directly above to slightly more intake valve side. I think they mainly created a looping path for the fuel that turns toward the spark plug during compression to make timing easier (a quick MSpaint of what i'm thinking):
I might be wrong, i'm not to trained in internal combustion, just going off some personal thought and learned physics. But to adapt DI to the rotary i was curious to the injector pressure because of the curved path of the rotor in compression towards ignition. A piston engine is 1 dimensional towards compression while a rotor is moving in 2 dimensions so i cannot think of a predictable path of injected fuel. Maybe thats while your friend wants 20K psi for instant atomized liquid fuel to a gas, which seems to erase the problem i'm thinking of in my head.
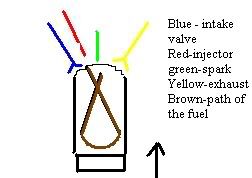
I might be wrong, i'm not to trained in internal combustion, just going off some personal thought and learned physics. But to adapt DI to the rotary i was curious to the injector pressure because of the curved path of the rotor in compression towards ignition. A piston engine is 1 dimensional towards compression while a rotor is moving in 2 dimensions so i cannot think of a predictable path of injected fuel. Maybe thats while your friend wants 20K psi for instant atomized liquid fuel to a gas, which seems to erase the problem i'm thinking of in my head.
#175
Registered User
Join Date: Oct 2005
Location: Toronto, Canada
Posts: 2,047
Likes: 0
Received 0 Likes
on
0 Posts
oh man, sorry, thanks for the correction, i dunno why i said diesel is fast burning, if it does it wouldnt have such a low rpm!.. my bad=/
________
BUBBLER PIPE
________
BUBBLER PIPE
Last edited by Renesis_8; 09-11-2011 at 10:34 AM.